Supply Chain Meaning
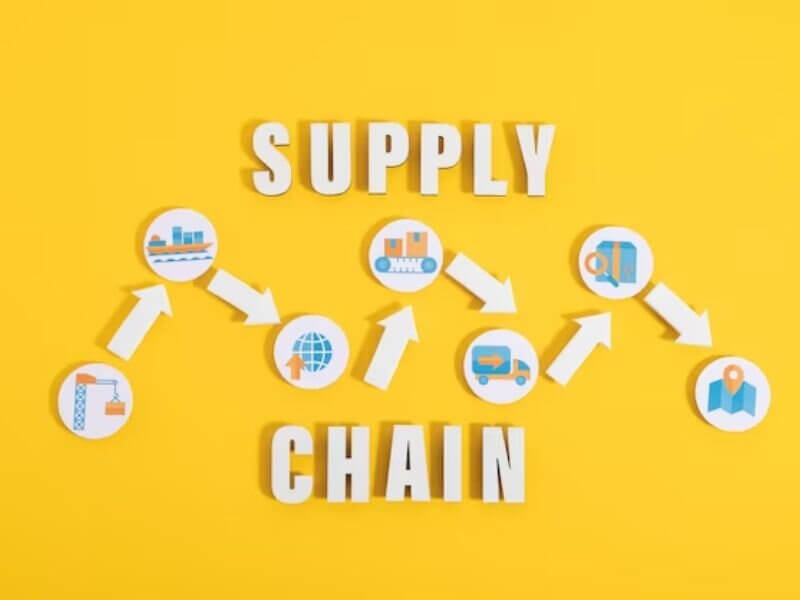
A supply chain is essentially the entire journey of a product, from sourcing of raw materials to manufacturing, storage, transportation, and delivery to the end customer. The primary goal of a supply chain is to efficiently and effectively deliver products or services to the consumer.
This involves things like planning, sourcing materials, production, distribution, and even returns. By effectively managing supply chains, companies can aim to reduce costs, improve efficiency, and get products to customers faster.
Supply Chain Meaning in Hindi
Supply Chain = आपूर्ति श्रृंखला
आपूर्ति श्रृंखला अनिवार्य रूप से एक उत्पाद की संपूर्ण यात्रा है, जिसमें कच्चे माल की सोर्सिंग से लेकर विनिर्माण, भंडारण, परिवहन और अंतिम ग्राहक तक डिलीवरी शामिल है। आपूर्ति श्रृंखला का प्राथमिक लक्ष्य उपभोक्ता तक सामान या सेवाओं को कुशलतापूर्वक और प्रभावी ढंग से वितरित करना है।
Supply Chain Meaning in Tamil
Supply Chain = விநியோக சங்கிலி
விநியோக சங்கிலி என்பது, மூலப்பொருட்கள் ஆதாரம் முதல் உற்பத்தி, சேமிப்பு, போக்குவரத்து மற்றும் இறுதி வாடிக்கையாளருக்கு வழங்குதல் வரையான, ஒரு பொருளின் முழுப் பயணமாகும். ஒரு விநியோகச் சங்கிலியின் முதன்மை குறிக்கோள், நுகர்வோருக்கு பொருட்களை அல்லது சேவைகளை திறமையாகவும் திறம்படமாகவும் வழங்குவதாகும்.
Logistics & Supply Chain Management
If you ask is logistics a part of supple chain management, yes, logistics is a crucial part of supply chain management. It focuses on the planning, implementation, and control of the flow and storage of goods, services, and related information between the point of origin and the point of consumption.
Logistics activities include transportation, warehousing, inventory management, packaging, and handling. Logistics plays a vital role in optimizing the movement of goods, ensuring timely delivery, and minimizing costs within the supply chain.
Supply Chain Management
Supply chain management (SCM) refers to the coordination and oversight of all activities involved in the planning, execution, and control of the supply chain.
It involves the integration of key business processes, from sourcing raw materials to delivering finished products to customers. SCM aims to enhance overall supply chain efficiency, responsiveness, and profitability.
Supply Chain Process
Planning:
The planning phase involves forecasting demand, setting production levels, and determining the required resources. It includes activities such as demand planning, inventory management, and production scheduling.
Sourcing:
Sourcing involves selecting and establishing relationships with suppliers to acquire the necessary raw materials, components, or services. It includes activities such as supplier selection, negotiation, and contract management.
Procurement:
Procurement is the process of purchasing goods or services from suppliers. It involves activities such as order placement, invoicing, and payment processing.
Production:
The production phase involves transforming raw materials into finished products. It includes activities such as manufacturing, quality control, and packaging.
Warehousing and Inventory Management:
Warehousing involves storing and managing inventory. It includes activities such as receiving, storage, picking, and packing. Inventory management focuses on optimizing inventory levels to meet customer demand while minimizing holding costs.
Delve deeper into the topic of warehouses and be a step ahead.
Transportation:
Transportation is the movement of goods from one location to another. It includes activities such as selecting carriers, route planning, shipment tracking, and managing transportation documentation.
Distribution:
Distribution involves delivering products to end customers. It includes activities such as order processing, order fulfilment, and managing customer relationships.
Customer Service:
Customer service is an essential aspect of the supply chain. It focuses on providing support to customers, addressing their inquiries, handling returns or exchanges, and ensuring overall customer satisfaction.
Performance Measurement:
Measuring supply chain performance is crucial to identifying areas for improvement. Key performance indicators (KPIs) are used to assess various aspects, such as cost efficiency, delivery time, inventory accuracy, and customer satisfaction.
Continuous Improvement:
Supply chain management is an ongoing process, and continuous improvement is necessary to adapt to changing market dynamics and customer expectations. It involves analyzing performance data, identifying opportunities for optimization, and implementing changes to enhance overall supply chain effectiveness.
By effectively managing these interconnected activities, supply chain management aims to streamline operations, minimize costs, improve customer satisfaction, and drive business success.
Example:
Let’s consider a multinational clothing brand that designs and manufactures its products in various countries. The supply chain begins with raw materials being sourced from different suppliers around the world.
These materials are then transported to manufacturing facilities, where they are transformed into finished products. Once the products are ready, they are packed and shipped to regional distribution centers strategically located to ensure efficient coverage.
From the distribution centers, the products are further dispatched to individual retail stores or directly to customers through online orders. Throughout the entire process, careful coordination is required to optimize transportation routes, manage inventory levels, and maintain timely delivery, ensuring that the right products reach the right locations at the right time while minimizing costs and maximizing customer satisfaction.
FAQs:
- How does supply chain management help improve customer satisfaction?
Supply chain management ensures timely delivery, efficient inventory management, and seamless coordination, resulting in improved customer satisfaction.
- How does logistics contribute to supply chain efficiency?
Logistics optimizes transportation, warehousing, and inventory management, reducing costs, minimizing lead times, and enhancing overall supply chain efficiency.
- What role does supply chain planning play in reducing costs?
Effective supply chain planning helps identify cost-saving opportunities, optimize production and inventory levels, and minimize waste, leading to cost reductions in the overall supply chain.